
Steel Manu-
facturing
We know steel like no one else.
Flexible, sustainable,
cost-efficient
From the automotive and energy sectors to mechanical engineering and construction – the whole world wants steel. We deliver it. Industry-specific, customer-specific – in all possible grades and standards. Whether DIN, EN, ASTM, API or others. If required, we can even develop our own steel grades for you, optimally matched to your applications. Because we know steel like no one else.
It all starts with the steel smelting process: A special treatment makes our steel ideal for dynamically stressed components, for example in automotive applications. During production, we meticulously check all parameters for you. This is how we meet your requirements, or even surpass them. In doing so, we also reduce our carbon footprint – for example with efficient production processes, the use of green electricity if required, and optimized internal processes and transport. The latter almost exclusively by train.
Video portrait:
Our steel workers
Video portrait:
Our steel workers
260 employees, annual capacity of 650,000 tons, high-quality steel from 100% scrap and environmentally friendly production: Andreas Stadtherr, head of the steel mill in Lingen, introduces his plant and his team.
85 % less CO₂ and
100 % recycling in steel production -
how does that work?
Efficient energy use, fewer emissions: Our electric steel plant in Lingen, for example, works with an electric arc furnace (EAF). We only process steel scrap. As a result, we avoid up to 85 % of direct CO₂ emissions compared with steel production in a conventional blast furnace.
As if that weren´t enough, we also recycle the scrap metal that accumulates during production. We can also provide seamless tube solutions that are suitable. Much to the delight of our customers.
How sustainable steel production works
Hot stuff – our steel production
How sustainable steel production works
Hot stuff – our steel production
At BENTELER we make steel billets or slabs from scrap. This scrap is melted down in our steel mill in the electric arc furnace using graphite electrodes. We then add additives and alloying elements to create exactly the type of steel you want. Finally, the steel is cast in the continuous caster. Whichever dimensions you need, the product is a piece of technological excellence.
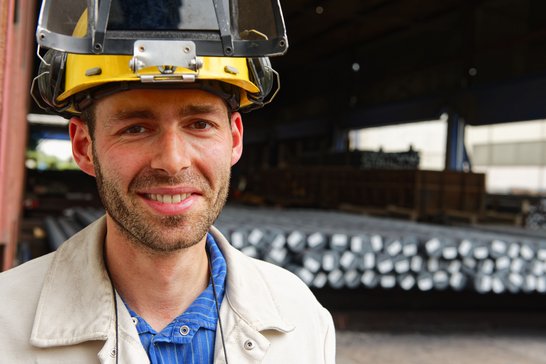
Individual steps:
steel production at the Lingen electric steel mill

Explanatory video:
Steel production in an electric arc furnace
Explanatory video:
Steel production in an electric arc furnace
Metallurgist Dominic Kehl explains how environmentally friendly steel production in an electric arc furnace works – and how we meet a wide range of customer requirements. By the way, it only takes about nine hours from delivery of the scrap to shipment of the new steel – sustainably by rail, of course.
Lighter with better
crash performance
Geometry, weldability, strength, toughness. We're well versed in combining material properties. For example, with our new innovative material BAH120plus® we’re supporting a renowned German commercial vehicle manufacturer in the area of crash management.
This material helps to significantly reduce the weight of the roll cages while offering better crash performance. That’s what we understand with unsurpassed metal expertise.